本分析では、石炭火力発電所の排ガス脱硫(FGD)システムを例に、従来のFGD排水システムにおける設計不良や高い機器故障率といった課題を検証しました。複数の最適化と技術改良により、排水中の固形分濃度が低減し、システムの正常な運転が確保され、運用・保守コストが削減されました。実用的な解決策と推奨事項が提示され、将来の排水ゼロ排出達成に向けた確固たる基盤が築かれました。
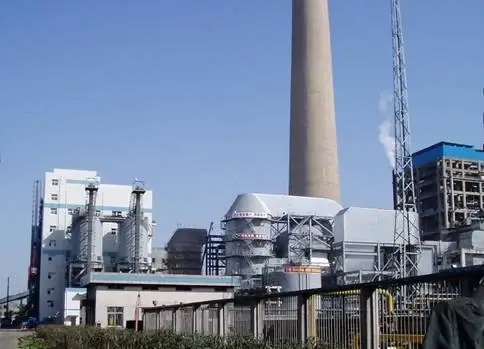
1. システムの概要
石炭火力発電所では、石灰石(CaCO₃)を吸収剤として用いる石灰石・石膏湿式FGDプロセスが一般的に採用されています。このプロセスでは、必然的にFGD廃水が発生します。このケースでは、2つの湿式FGDシステムが1つの廃水処理ユニットを共有しています。廃水源は石膏サイクロンのオーバーフローで、従来の方法(3槽式)で処理され、設計処理能力は22.8t/hです。処理済みの廃水は、粉塵抑制のため6km離れた処分場までポンプで送られます。
2. 当初のシステムにおける主な問題点
薬液注入ポンプのダイヤフラムは漏れや故障が頻繁に発生し、薬剤の連続注入が不可能でした。プレートフレーム式フィルタープレスとスラッジポンプの故障率が高いため、労働力が増加し、スラッジ除去が阻害され、浄化槽での沈殿が遅くなっていました。
石膏サイクロンのオーバーフローから排出された排水は、密度約1,040 kg/m³、固形分濃度3.7%でした。このため、処理水の連続排出と吸収槽内の有害イオン濃度の制御がシステムから阻害されていました。
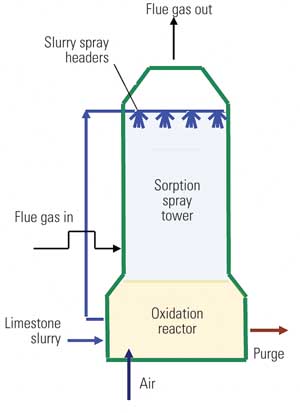
3. 予備的な変更
化学物質の投与量の改善:
重力制御による一貫した投与を保証するために、トリプルタンクシステムの上に追加の化学薬品タンクが設置され、オンライン濃度計.
結果:水質は改善したが、沈殿処理は依然として必要だった。1日あたりの排出量は200m³に減少したが、これは2つのFGDシステムの安定稼働には不十分だった。注入コストは平均12元/トンと高かった。
粉塵抑制のための廃水の再利用:
浄化槽の底にポンプが設置され、廃水の一部を敷地内の灰サイロに送り、混合と加湿を行います。
結果: 処分場への圧力は軽減されましたが、依然として濁度が高く、排出基準を満たしていません。
4. 現在の最適化対策
環境規制が厳しくなるにつれ、さらなるシステムの最適化が必要になりました。
4.1 化学調整と連続運転
化学薬品の投与量を増やすことでpHを9~10に維持しました。
1日の使用量:石灰(45kg)、凝固剤(75kg)、凝集剤。
断続的なシステム運転後、1日あたり240 m³の清水の排出を確保しました。
4.2 緊急スラリータンクの再利用
緊急タンクの二重使用:
ダウンタイム中:スラリー保管。
運転中:清澄な水抽出のための自然沈殿。
最適化:
柔軟な操作を可能にするために、さまざまなタンクレベルにバルブと配管を追加しました。
沈殿した石膏は脱水または再利用のためにシステムに戻されました。
4.3 システム全体の変更
真空ベルト脱水システムからの濾液を廃水バッファタンクにリダイレクトすることで、流入する廃水中の固形物濃度を下げました。
緊急タンクに化学薬品を注入することで自然沈降時間を短縮し、沈殿効率を高めます。
5. 最適化のメリット
容量の向上:
毎日 400 m³ を超える基準廃水を排出しながら連続運転します。
吸収器内のイオン濃度を効果的に制御します。
簡素化された操作:
プレート&フレームフィルタープレスが不要になりました。
汚泥処理の労力を軽減します。
強化されたシステム信頼性:
廃水処理スケジュールの柔軟性が向上します。
機器の信頼性が向上。
コスト削減:
化学薬品の使用量は、石灰(1.4 kg/t)、凝固剤(0.1 kg/t)、凝集剤(0.23 kg/t)に削減されました。
処理コストは5.4元/トンに低下しました。
化学薬品コストを年間約948,000元節約。
結論
FGD排水システムの最適化により、効率が大幅に向上し、コストが削減され、より厳しい環境基準への適合も実現しました。これらの対策は、排水ゼロと長期的な持続可能性の実現を目指す同様のシステムにとって参考となるでしょう。
投稿日時: 2025年1月21日